This is just a fast taste of what is happening at Smeltfest. Sorry there are no images, with the confusion of working from the road, my camera cables are up at the workshop this morning.
The first day in the later afternoon and evening was really scheduled as a travel day. As people arrived, we cleared off the large 'Africa' furnace from last year. Another long task was roasting and crushing ore for this year's series.
The first official day started with preparing charcoal, with several hundred pounds worth to be hauled, crushed, sized and screened. Others worked on preparing Lee Sauder's production smelter for use. A third group worked up clay mixture for the various small furnaces and hearths under consideration this year. Skip Williams supervised the construction of an Aristotle re-melting furnace. I worked at all these tasks to some degree. Later in the afternoon, I showed Therese Kearns (an archaeologist participating from England) how the Aristotle worked. In the background from about noon on, Lee and Jesus Herandez ran a test smelt of the magnetite ore prepared the day before.
The second full day started with the preparation for another smelt using a different magnetite ore. Insights (??) from the first smelt were applied to the second. (It was decided that we had done too good a job high grading the ore the day before, resulting in virtually no slag bath in the furnace.) Again this started with ore crushing while the furnace was given some minor repairs and generally set up. Just after lunch we started this second smelt. Therese and I undertook the charging cycles, with Lee making the control decisions. (This makes smelt 50 for me.) The experience from the day before obviously paid off - sort of. The iron ore was most definately reduced to metal, but the result was a higher carbon cast iron rather than a forgeable bloom.
This turned out to be not the problem it might of been, as Jesus was interested in examining a theoretical Japanese sequence. He explained that historical blades were visibly different than those using even the 'traditional' Tatara method (post 1700). The theory is that ore was converted into a cast iron, then that was placed in a secondary hearth set up to *reduce* the overall carbon content as billets were created. In the background, Jesus, Shelton Browder and Steve Mankowski constructed a medium sized refining hearth to test just this method. (Expected to run on day three).
Of course there is always a lot of mixed conversation between various of the assembled team. These off the cuff discussions are always extremely valuable for how we share insights, experiences - and common problems to us all.
(I may edit this posting later when I get some images ready to insert)
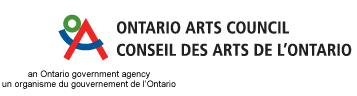
February 15 - May 15, 2012 : Supported by a Crafts Projects - Creation and Development Grant
COPYRIGHT NOTICE - All posted text and images @ Darrell Markewitz.
No duplication, in whole or in part, is permitted without the author's expressed written permission.
For a detailed copyright statement : go HERE
No comments:
Post a Comment